Why Your Warehouse Should Implement a Pick & Pack Process
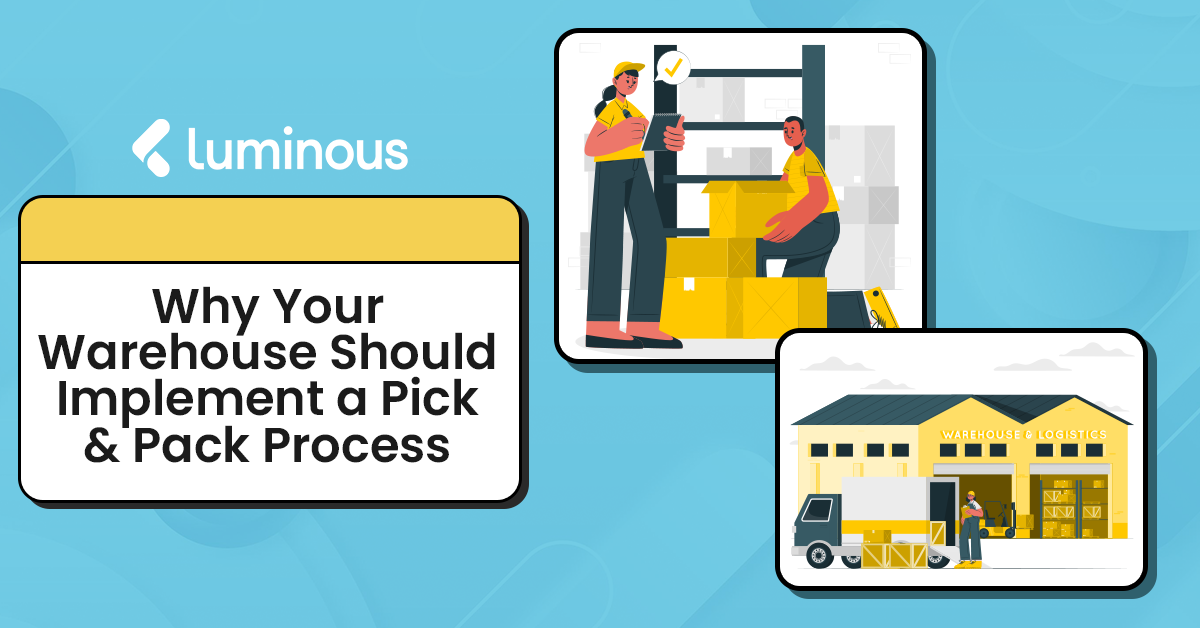
Cases for Pick and Pack
A study by the Aberdeen Group found that companies that implemented a pick and pack process experienced a 20% increase in order accuracy and a 35% reduction in order cycle time. The study also found that companies that implemented a pick and pack process were able to process 2-3 times more orders per day than those that did not.
In a separate study by the Warehousing Education and Research Council, it was found that implementing quality assurance processes in the pick and pack process can lead to a reduction in errors of up to 50%. The study also found that the use of quality assurance processes can help to reduce the amount of time spent on returns and exchanges, leading to a reduction in costs.
Another study by the Material Handling Industry of America found that companies that implemented a pick and pack process experienced a 50% reduction in order processing time and a 40% reduction in labor costs.
These studies demonstrate the significant benefits of implementing a pick and pack process and quality assurance in the warehouse. By implementing these processes, warehouses can increase efficiency, improve accuracy, and reduce costs associated with order fulfillment.
Why Choose Pick and Pack?
There are several reasons why a warehouse should choose to implement a pick and pack process. First and foremost, implementing this process can help to increase efficiency and improve order fulfillment accuracy. With a pick and pack process in place, warehouse staff can quickly and accurately locate items in the warehouse and pack them for shipping, leading to faster order turnaround times and increased customer satisfaction.
Additionally, implementing a pick and pack process can help to reduce costs associated with order fulfillment. By reducing the amount of time it takes to fulfill orders and improving order accuracy, warehouses can reduce labor costs and the costs associated with returns and exchanges.
Luminous Pick and Pack Module
Luminous is a cloud-based warehouse management system that offers a pick and pack module to help warehouses streamline their order fulfillment process. The module includes features such as scanning, real-time inventory tracking, and quality assurance checks to ensure accurate order fulfillment.
With Luminous' pick and pack module, warehouses can reduce the amount of time it takes to fulfill orders, increase order accuracy, and reduce the costs associated with returns and exchanges. Additionally, the module includes real-time inventory tracking, allowing warehouse staff to quickly locate and retrieve items from the warehouse.
Conclusion
In conclusion, implementing a pick and pack process and quality assurance in the warehouse offers numerous benefits, including increased efficiency, improved accuracy, and reduced costs. Studies have shown that companies that implement these processes can experience significant improvements in order accuracy, order cycle time, and labor costs.
By choosing to implement a pick and pack process, warehouses can improve their order fulfillment process and increase customer satisfaction. And with Luminous' pick and pack module, warehouses can streamline their order fulfillment process, reduce mistakes, and improve inventory accuracy.