Key Metrics to Measure From Pick and Pack Operations
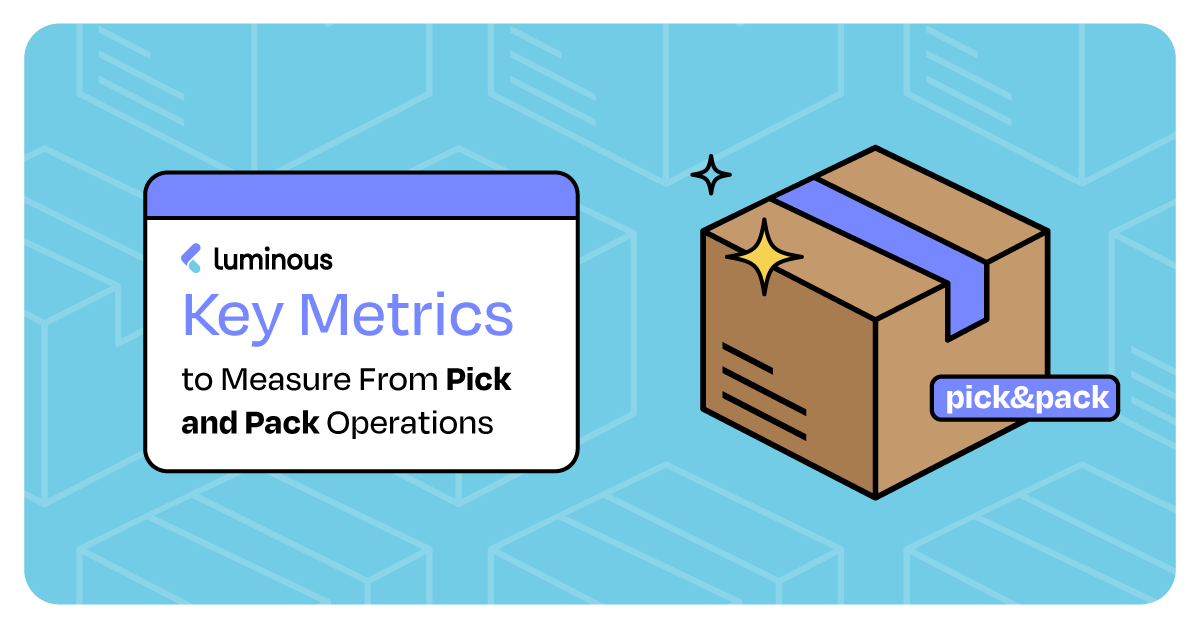
In the fast-paced world of warehousing and logistics, staying on top of your pick and pack operations is crucial for success. To continuously improve efficiency, reduce errors, and enhance customer satisfaction, you need to measure and analyze various aspects of your pick and pack processes. In this article, we'll dive into seven essential metrics that can provide valuable insights into the performance of your pick and pack operations.
Order Accuracy Rate
Order accuracy is a critical metric that directly impacts customer satisfaction and operational costs. To calculate the order accuracy rate, divide the number of accurately picked and packed orders by the total number of orders fulfilled within a specific time frame. A high accuracy rate indicates that your pick and pack processes are effective, reducing the likelihood of returns and customer complaints.
Pick and Pack Cycle Time
Cycle time measures the average duration it takes to complete the entire pick and pack process for a single order, from the moment an order is received until it's ready for shipment. Monitoring cycle time helps you identify bottlenecks and inefficiencies in your operations. Reducing cycle time can lead to faster order fulfillment and improved customer satisfaction.
Inventory Accuracy
Inventory accuracy is crucial for preventing stockouts, overstock situations, and discrepancies between your records and physical inventory. This metric measures the percentage of inventory items that match your records. Regularly auditing your inventory and tracking discrepancies can help maintain high levels of accuracy and prevent costly inventory issues.
Fill Rate
Fill rate calculates the percentage of customer orders that are fulfilled completely from the available stock. A high fill rate indicates that you're consistently meeting customer demand without requiring backorders or partial shipments. It's a key metric for assessing your ability to keep customers satisfied and avoid potential order delays.
Order Turnaround Time
Order turnaround time measures the time it takes for an order to move through your pick and pack processes and leave your facility. It encompasses order processing, picking, packing, and shipping. Reducing order turnaround time enhances customer satisfaction, especially for customers who prioritize fast delivery.
Error Rate
The error rate metric tracks the percentage of orders that contain errors, such as incorrect items, quantities, or shipping addresses. Reducing the error rate is essential for minimizing returns, customer complaints, and additional shipping costs. Regularly monitoring this metric allows you to pinpoint areas in need of improvement within your pick and pack operations.
Cost per Order
Cost per order is a financial metric that calculates the average cost associated with processing and fulfilling a single order. This metric considers labor costs, packaging materials, shipping expenses, and other operational costs. Reducing the cost per order while maintaining or improving service quality is a key goal for optimizing your pick and pack operations.
Conclusion
In the world of warehousing and logistics, continuous improvement is essential for staying competitive and meeting customer expectations. These seven metrics - order accuracy rate, pick and pack cycle time, inventory accuracy, fill rate, order turnaround time, error rate, and cost per order - provide valuable insights into the performance of your pick and pack operations. By regularly tracking and analyzing these metrics, you can identify areas for improvement, optimize processes, and ultimately enhance your warehouse's efficiency and customer satisfaction. Remember, measuring is just the first step; taking action based on these metrics is where you'll see the most significant improvements in your operations.